Rubber Preformers (Barwell)
Preforming (Barwell) machines are essential for preparing rubber compounds for the press-vulcanization process. These machines efficiently create preform parts for compression presses, offering numerous advantages:
- High Production Volume: Ideal for rubber parts requiring large-scale production.
- Weight Precision: Ensures accurate unit grammage in rubber parts.
- Quality and Waste Reduction: Delivers high preform quality with minimal waste.
- Process Efficiency: Enhances ease of process, automation, and workmanship.
Preforming (Barwell) machines are essential for preparing rubber compounds for the press-vulcanization process. These machines efficiently create preform parts for compression presses, offering numerous advantages:
- High Production Volume: Ideal for rubber parts requiring large-scale production.
- Weight Precision: Ensures accurate unit grammage in rubber parts.
- Quality and Waste Reduction: Delivers high preform quality with minimal waste.
- Process Efficiency: Enhances ease of process, automation, and workmanship.
Preforming machines, which can be customized to meet specific customer needs, are typically classified by their cylinder diameter and the amount of compound they can accommodate. Standard cylinder diameters include:
- 100mm
- 125mm
- 150mm
- 200mm
- 250mm
- 300mm
Special sizes can also be manufactured as required. The capacity for a compound varies depending on its density.
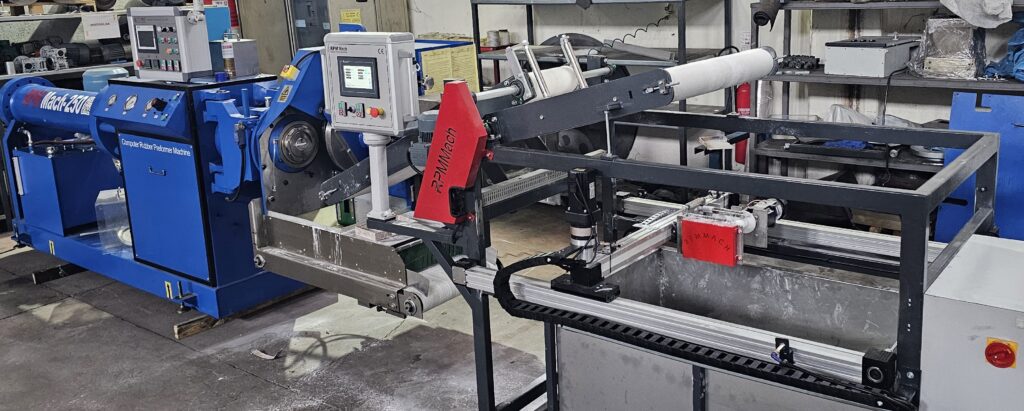
A key feature of the preforming machines designed by RPMMACH is their ability to automatically adjust product weight and precision. This is achieved through a special precision scale integrated into the machine, ensuring consistent and accurate results.
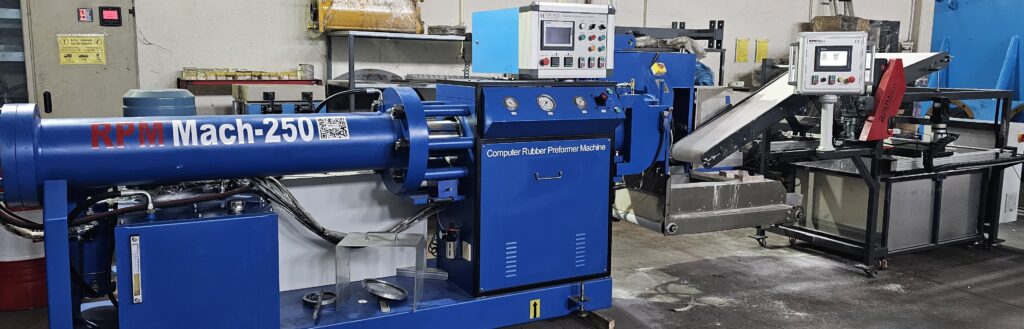
During the process, an integrated scale rechecks the weight of the cut pieces, ensuring accuracy at every step. The entire process flow is seamlessly controlled from the PLC screen of the machine, providing users with an intuitive and efficient interface.
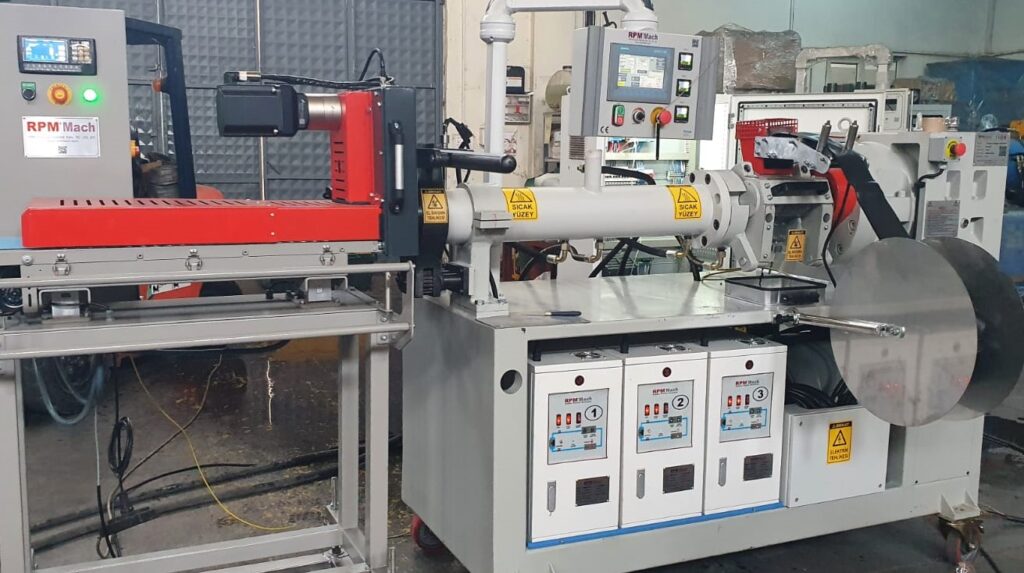
What sets the RPMMACH Preforming Machine apart is its innovative design, featuring a second ram inside the pusher ram. This unique mechanism continuously and precisely adjusts the stability of the rubber compound pressure, ensuring that the compound is consistently delivered to the mold at the same pressure.
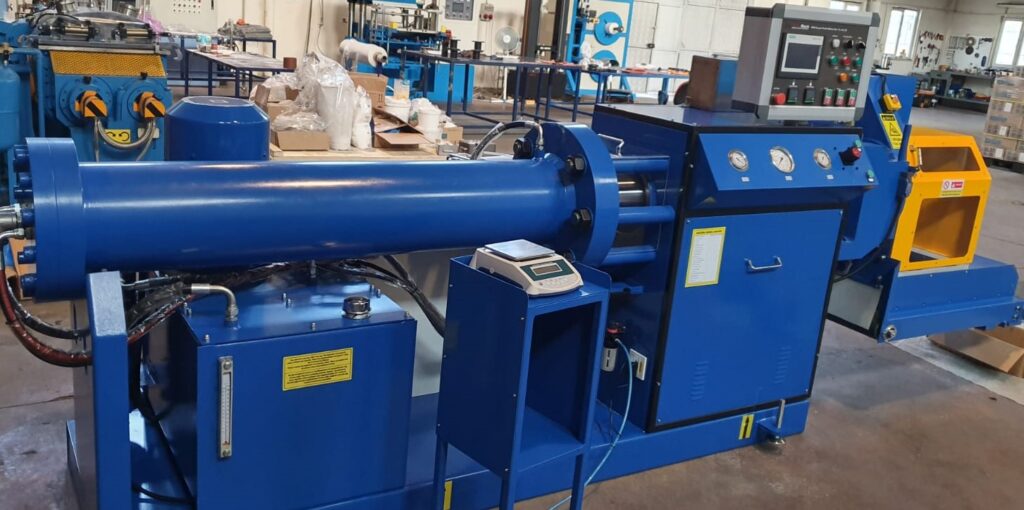
When the machine is stopped suddenly, it retracts with the main ram to the required extent, preventing the rubber compound from flowing out of the mold due to its own static pressure. This feature is crucial for the protection and safety of the cutting blades.
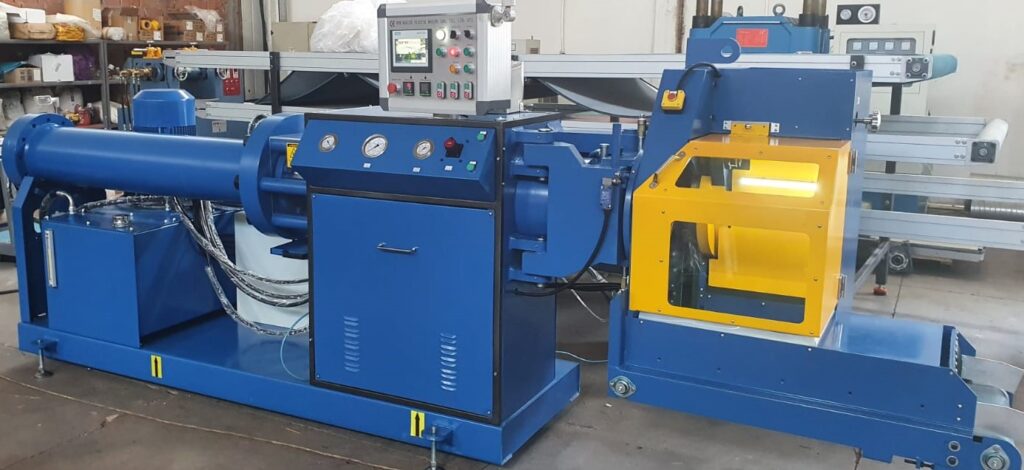
This machine is equipped with a maximum safety system, significantly reducing the possibility of user accidents. The standard option DEGASSING system effectively prevents pore-gas formation in the rubber part. Additionally, the internal heating system in the machine cylinder allows for the use of cold compounds. The machine also comes with standard options such as single or double blade configurations and an easy mold attachment-disassembly hydraulic system.
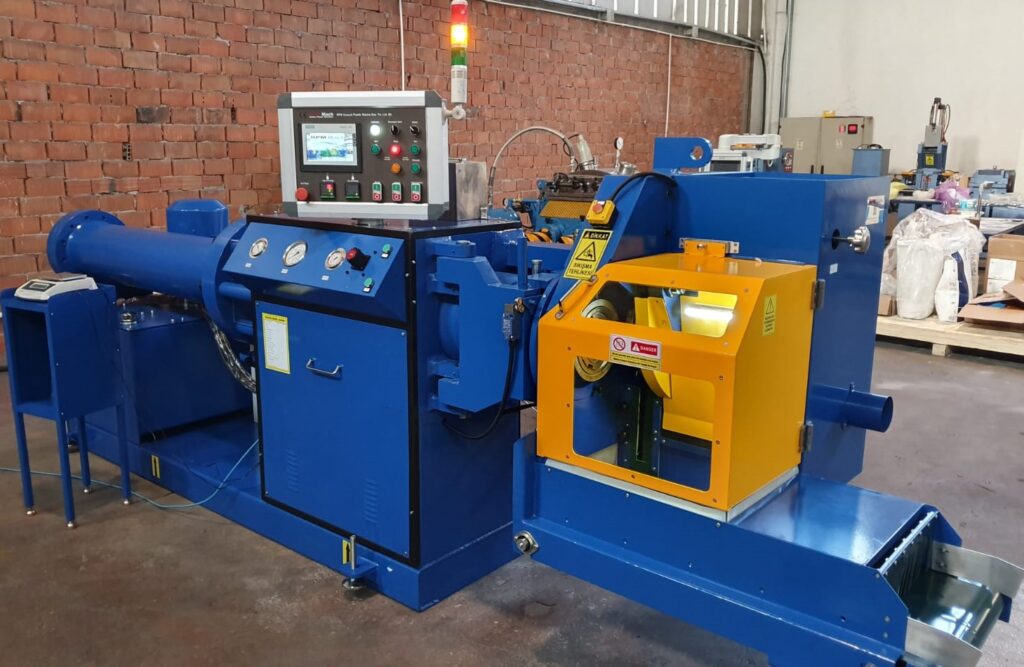
For companies with high production speeds, an optional belt-batch off water cooling system can be installed at the machine exit for instant cooling of pre-shaped parts.
Our preforming machines are designed to meet the highest standards, ensuring optimal performance and reliability in your production processes.