Rubber Banbury MIxers
Banbury mixers play a crucial role in the rubber industry, efficiently blending chemicals used in rubber formulations through mechanical pressure. This process transforms the ingredients into uniform compounds. The quality of mixing in Banbury mixers directly impacts the overall product quality and process efficiency. Achieving a homogeneous dispersion in Banbury mixers ensures consistent physical and dimensional properties in subsequent processes and the final product.
In rubber formulations, a variety of chemical materials with different forms and properties are used. These include liquid chemicals, powder chemicals, semi-masterbatch granular chemicals, polymers, acidic derivatives, and components with varying densities. All these materials are added to the same batch and expected to mix as homogeneously as possible. While achieving this level of homogeneity is physically challenging, especially considering the chemical reactions that can complicate the process, it remains the most critical step in rubber manufacturing.
At RPMMACH, we understand these mixing challenges and leverage our extensive experience to address them. We continuously enhance the design and construction of our Banbury mixers to ensure optimal performance, resulting in highly effective mixing processes and superior product quality.
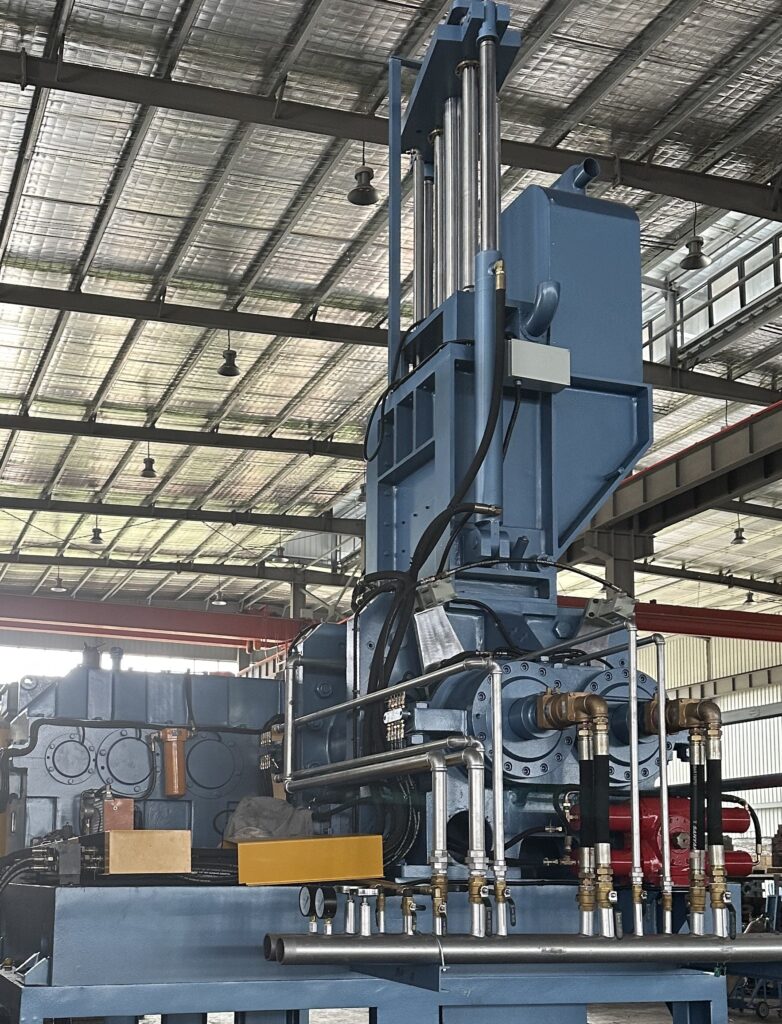
Optimizing Mixing Homogeneity In Banbury Mixers
The rotor types are the most crucial components affecting the mixing homogeneity in Banbury mixers. Over the years, various rotor models have been tested, and leading companies worldwide have conducted significant research in this area. Designs have included half-spiral-tangential wings on the rotor shaft, configurations with 2, 3, or 4 flat wings, and adjustable rotor speeds. Each of these innovations has proven beneficial, but they are often more suited to specific polymer processes. It’s important to note that no single rotor type or Banbury mixer can deliver optimal results for all polymers.
At RPMMACH, we recognize the importance of selecting the right rotor type for each unique application. Our ongoing research and development efforts focus on enhancing rotor designs to achieve the best possible mixing homogeneity for a wide range of polymers.
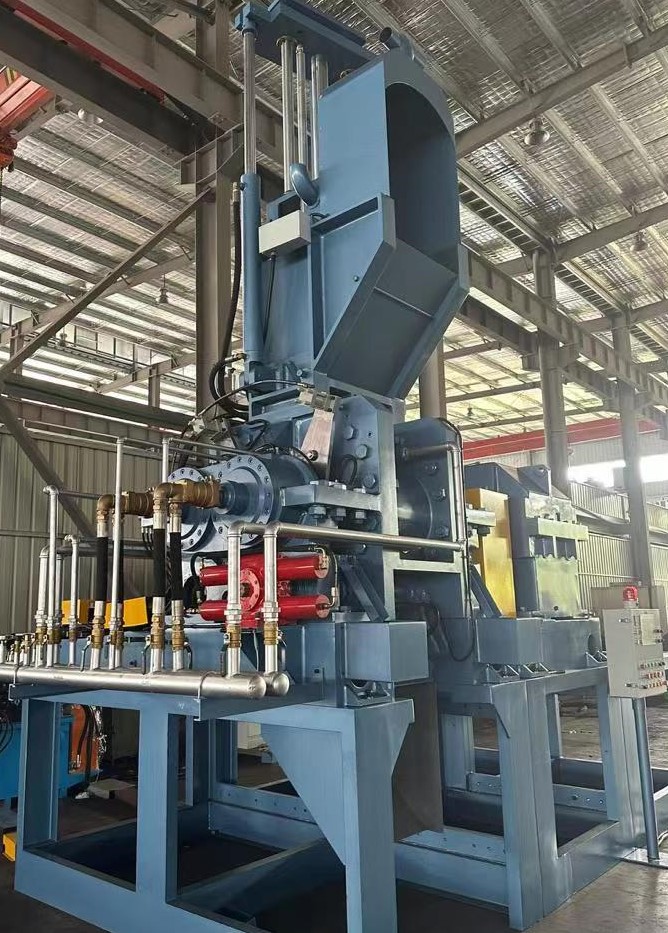
Innovative Intermash Rotors For Superior Mixing Homogeneity
Recent advancements have led to the development of the INTERMESH type rotor, which generally achieves near-homogeneous mixing results for all polymer mixtures. RPMMACH has designed its own intermesh rotor and secured a patent for this innovative design. While slightly more expensive than other options, we strongly recommend Banbury buyers consider the INTERMESH rotor for its superior performance.
Our company representatives are always available to provide detailed information on selecting the optimal Banbury configuration based on your specific needs and the polymers you work with.
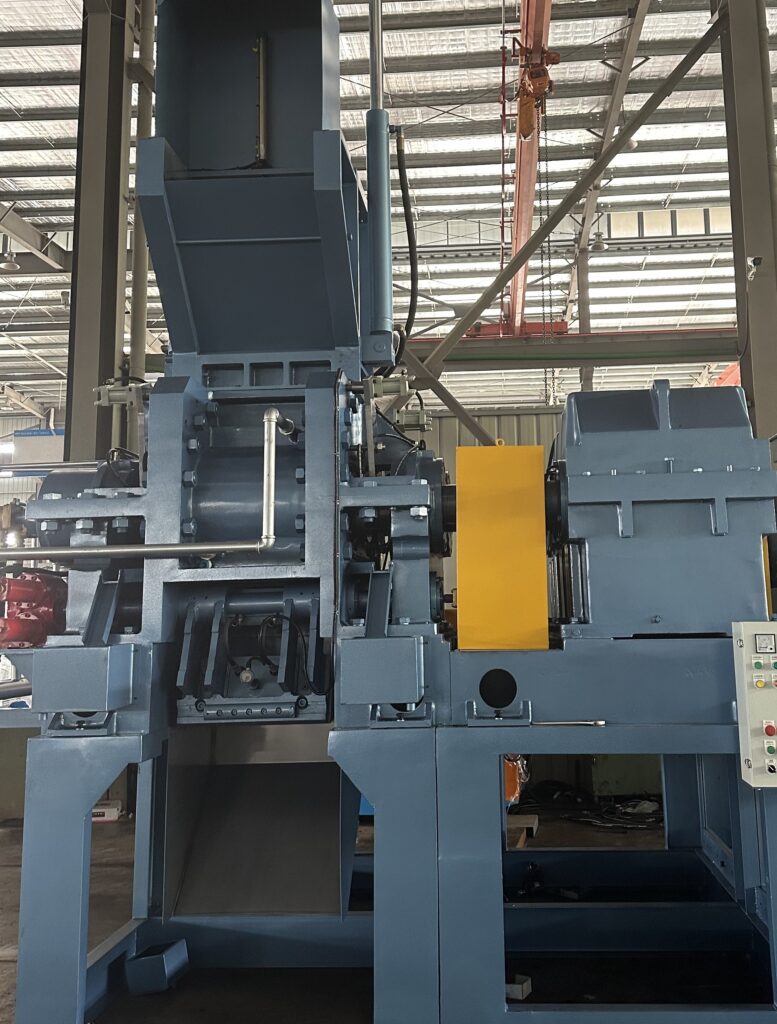
Advanced Cooling Systems For Optimal Banbury Performance
In addition to rotor design, the cooling system in Banbury mixers is crucial. While the temperature of the cooling water is a key factor, the machine’s design also plays a significant role. RPMMACH has successfully developed a system that ensures ideal water circulation in the mixing chamber, inside the rotors, and to the RAM (Press). This system operates at the optimal cycle and pressure, enhancing the overall efficiency and performance of the mixing process.
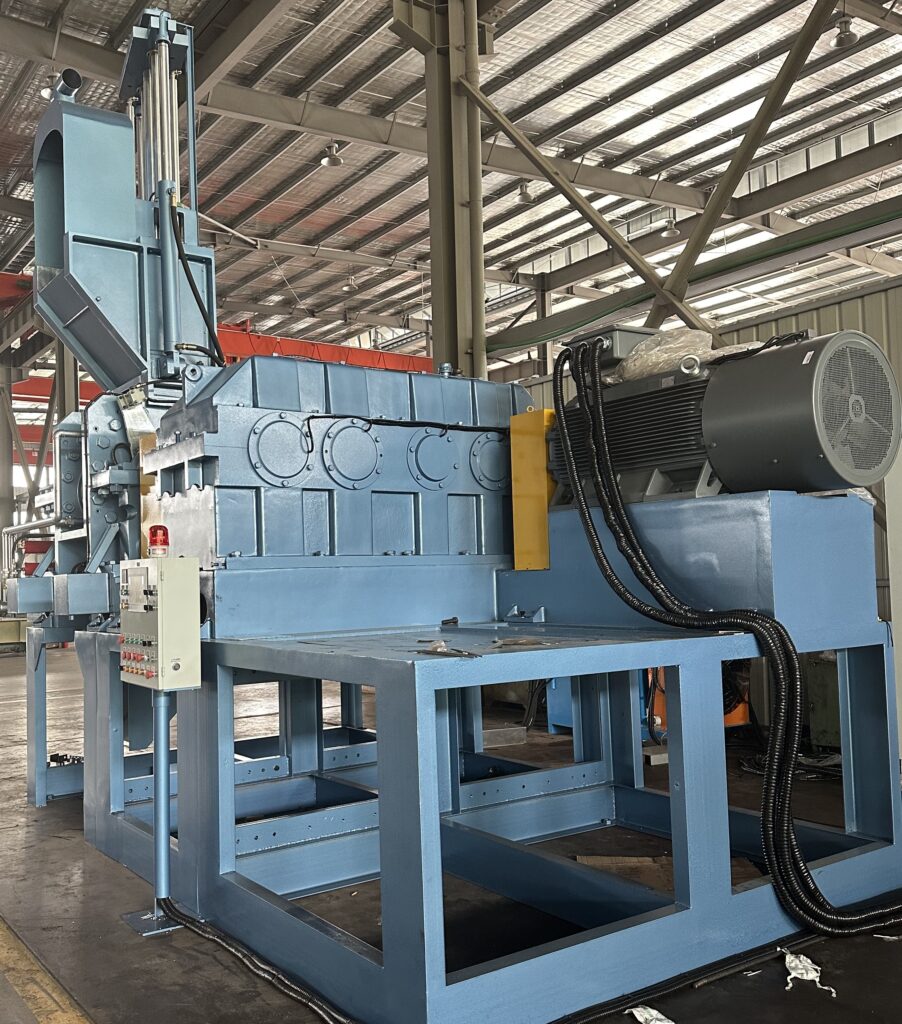
Advanced Banbury Mixing Solutions By RPMMACH
At RPMMACH, we understand the critical role of Banbury mixers in the rubber and chemical industries. Our Banbury mixers are designed to handle the intense pressure during the mixing process, utilizing a specialized system to prevent chemical leaks from the rotor bearings. This feature is essential for maintaining the integrity and efficiency of the mixing process.
Our Banbury mixers offer adjustable rotor speeds through a PLC control system, allowing for precise control over the mixing process. This is particularly beneficial when removing cooking chemicals or enhancing the mixing capabilities of certain compounds. Additionally, when integrated with automatic dosing units, these systems work seamlessly together to optimize your production process.
At RPMMACH, we ensure the highest quality for all our machines, including Banbury mixers. Before delivery and installation, each Banbury mixer undergoes rigorous operation and process tests. We measure the homogeneity of these tests using advanced carbon distribution devices and share the results with our customers in advance, ensuring transparency and confidence in our products.
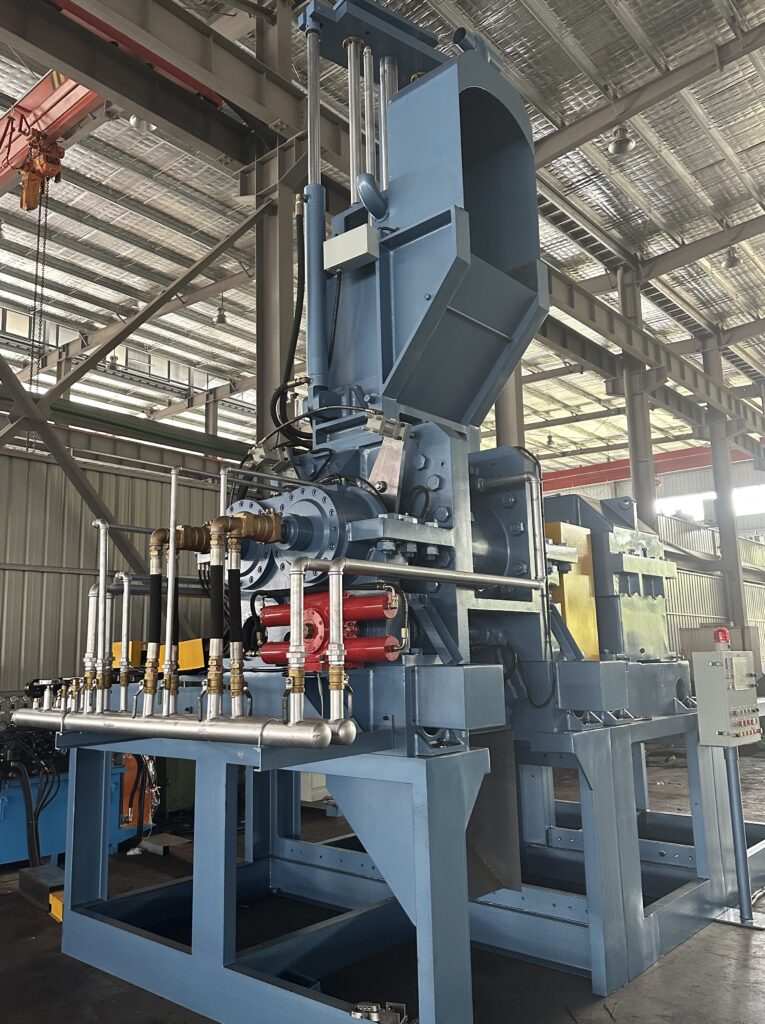