Rubber Kneader MIxer
Innovative Mixing Solutions for the Rubber Industry, At RPMMACH, we specialize in the design and manufacture of advanced rubber kneader mixers. Our machines are engineered to meet the highest standards of efficiency and reliability, ensuring optimal performance for your rubber mixing needs.
Hydraulic RAM is standard on our Kneader Mixers which can increase the homogenization quality and reduce mixing time.
By focusing on in-house development, we ensure that our machines meet the highest standards of quality and are tailored to the specific needs of our clients.
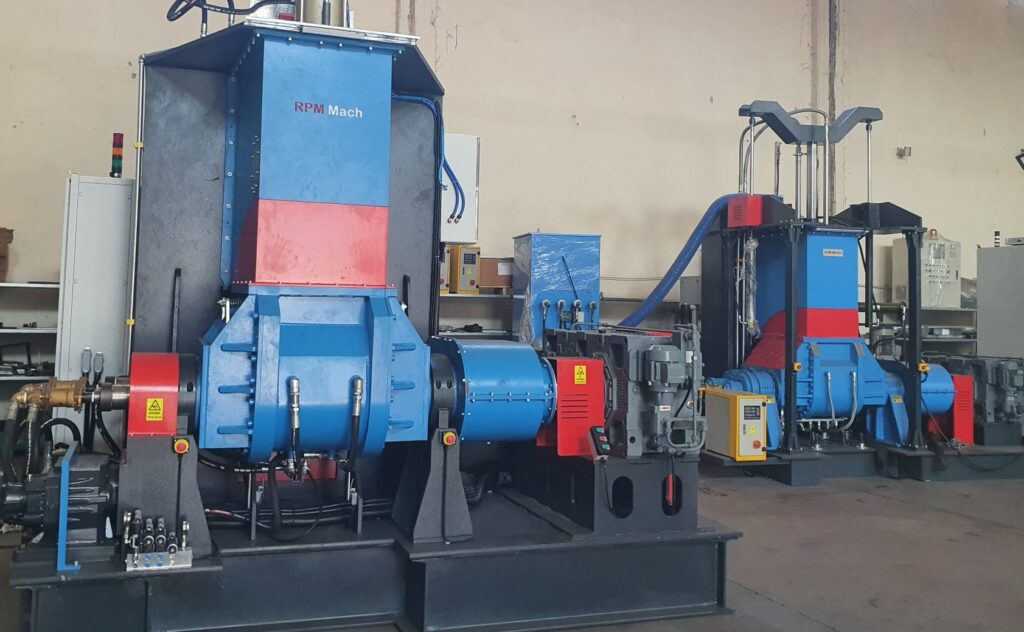
Enhanced Rubber Mixing
At RPMMACH, we pride ourselves on our rubber kneader mixers, featuring the patented INTERMESH rotor application. Since 2009, we have been revolutionizing the industry, producing rubber kneader mixers equipped with this advanced rotor technology.
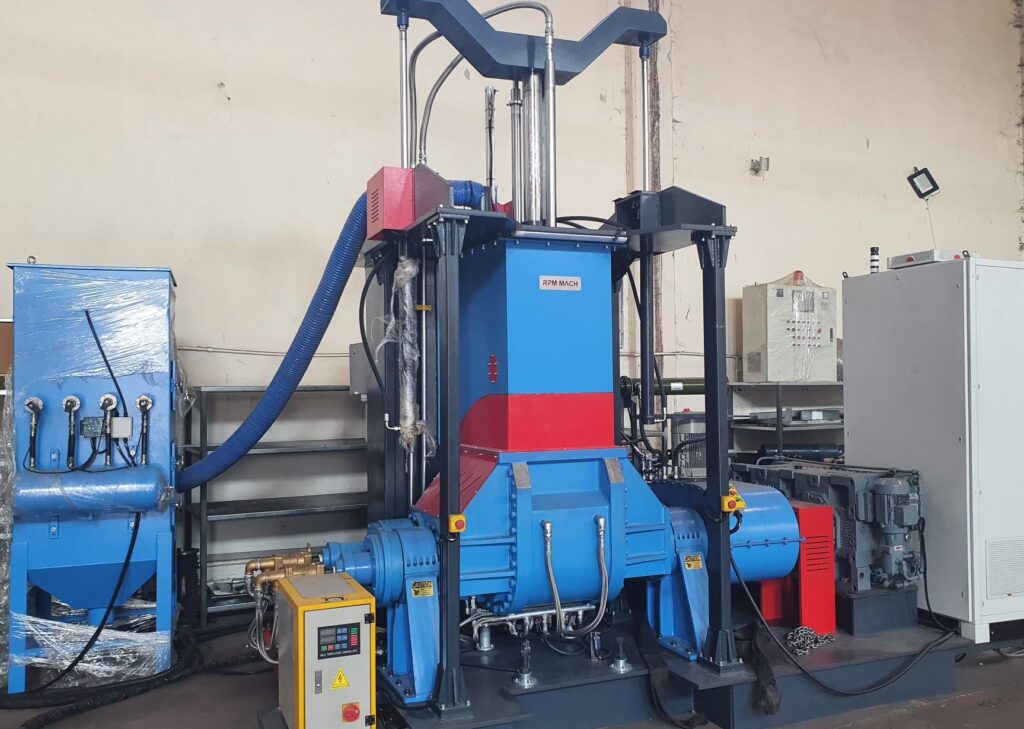
The INTERMESH rotor design significantly enhances mixing quality, speed, and dispersion, outperforming other rotor types. This innovation is crucial for achieving optimal homogenization in rubber formulations, as the rotor structure plays a decisive role in the mixing process.
While traditional kneader-type rubber mixers typically use tangential 2-wing rotors, RPMMACH has pioneered the development and implementation of 3-wing and intermesh rotor types. These advancements ensure superior performance and efficiency in our rubber mixers, setting a new standard in the industry.
The traditional 2-wing tangential rotor type, while effective for EVA and similar plastic derivatives, often falls short in performance and efficiency for NR (Natural Rubber) and synthetic rubber (EPDM, NBR, CR, IR, BR, etc.) mixtures. Recognizing this, RPMMACH has revolutionized rotor design to significantly boost the performance of rubber mixers.
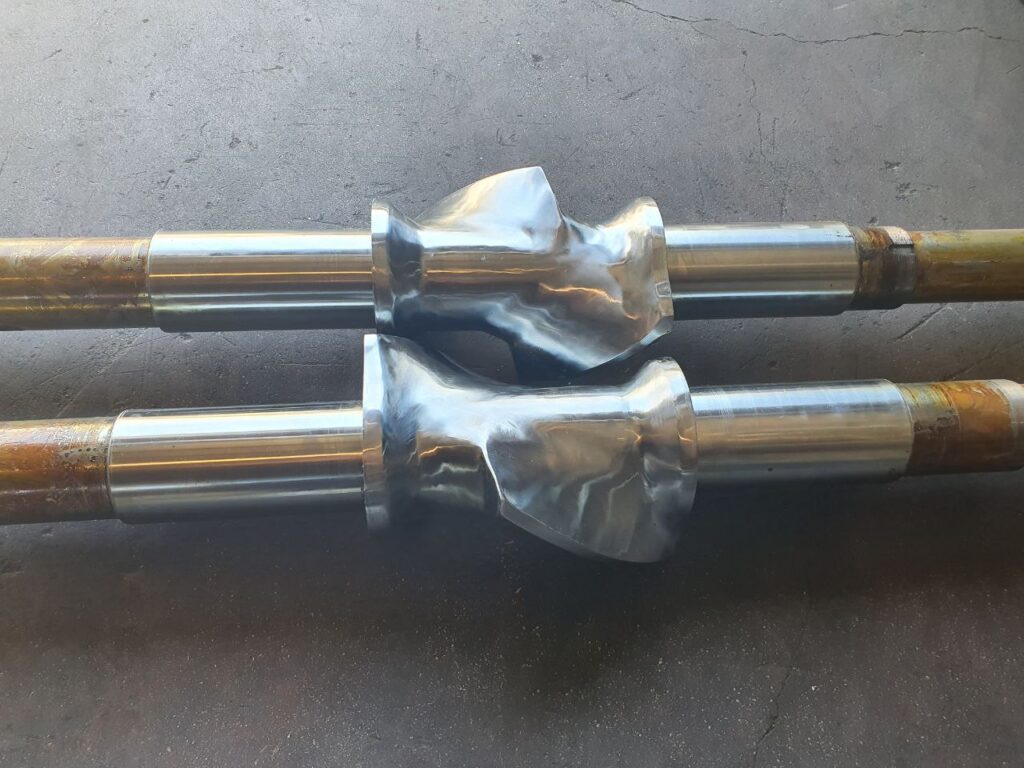
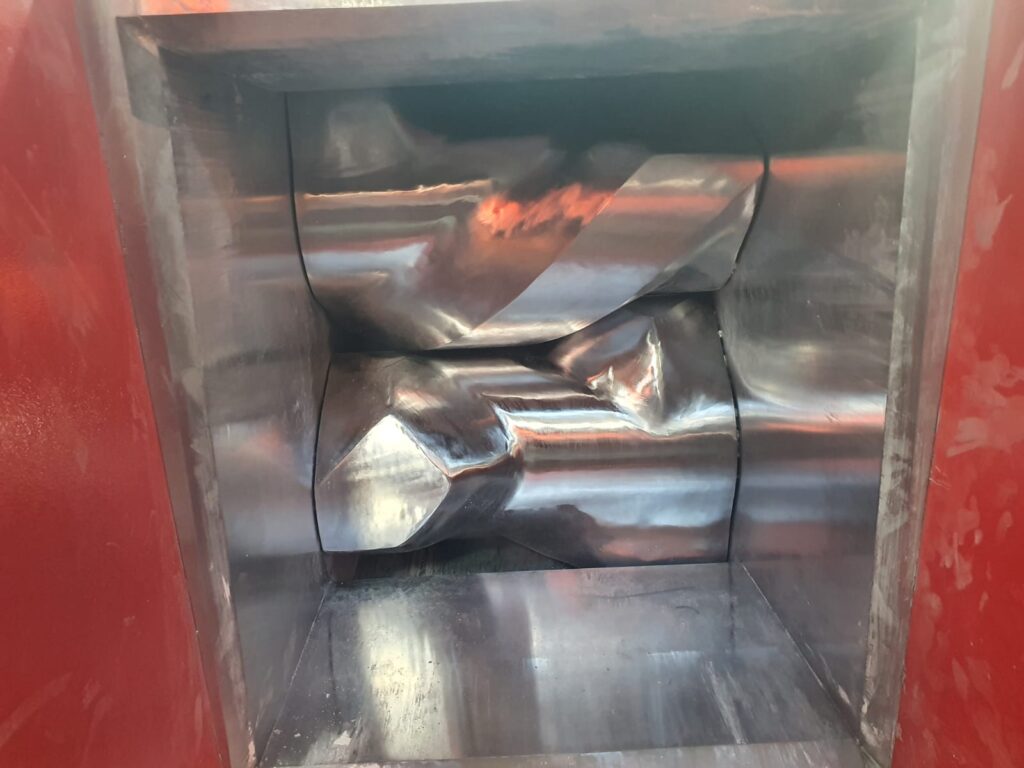
Superior Sealing And Clean Mixing Environment
ONE of the standout features of RPMMAH’s rubber mixers is the exceptional sealing quality for both powdered and liquid materials during the mixing process. Our mixers are equipped with sealing plates made from a specialized material used in the rotor bearings within the mixing chamber. This prevents any leakage of materials, ensuring a clean and efficient mixing process.
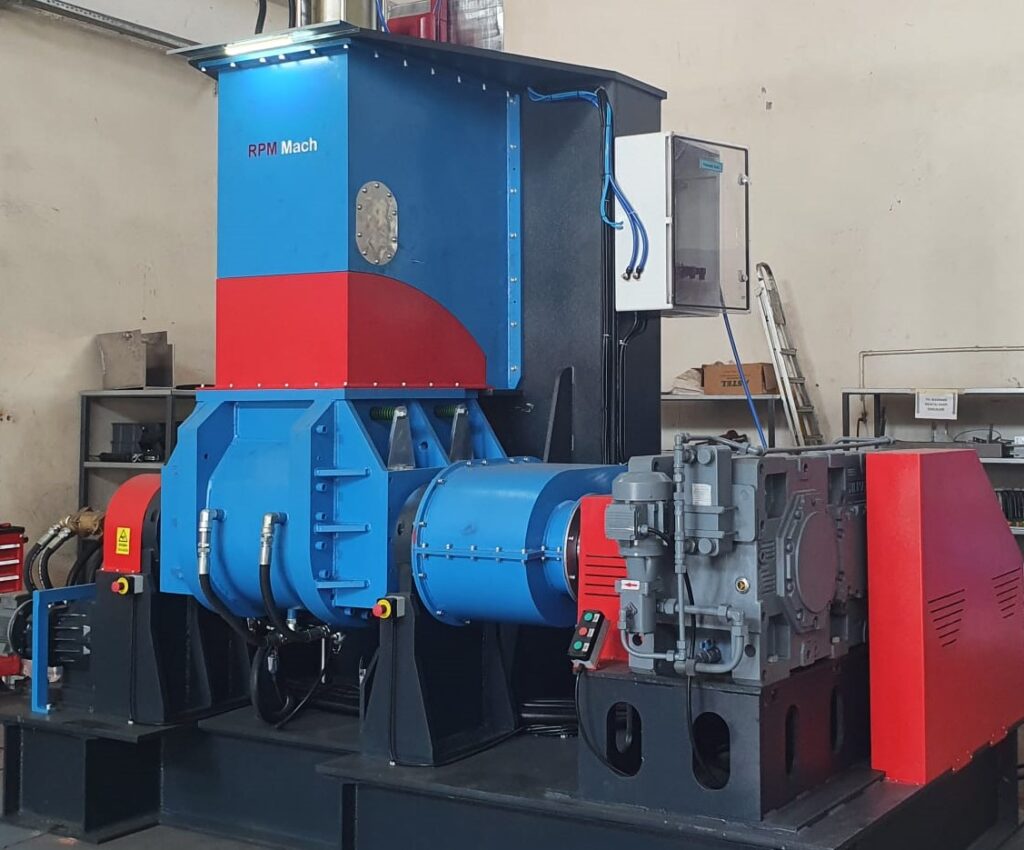
Internal dust generated by RAM movement during mixing is effectively managed. Our optional Dust Removal Unit collects and transforms this dust, further enhancing the cleanliness of the mixing environment.
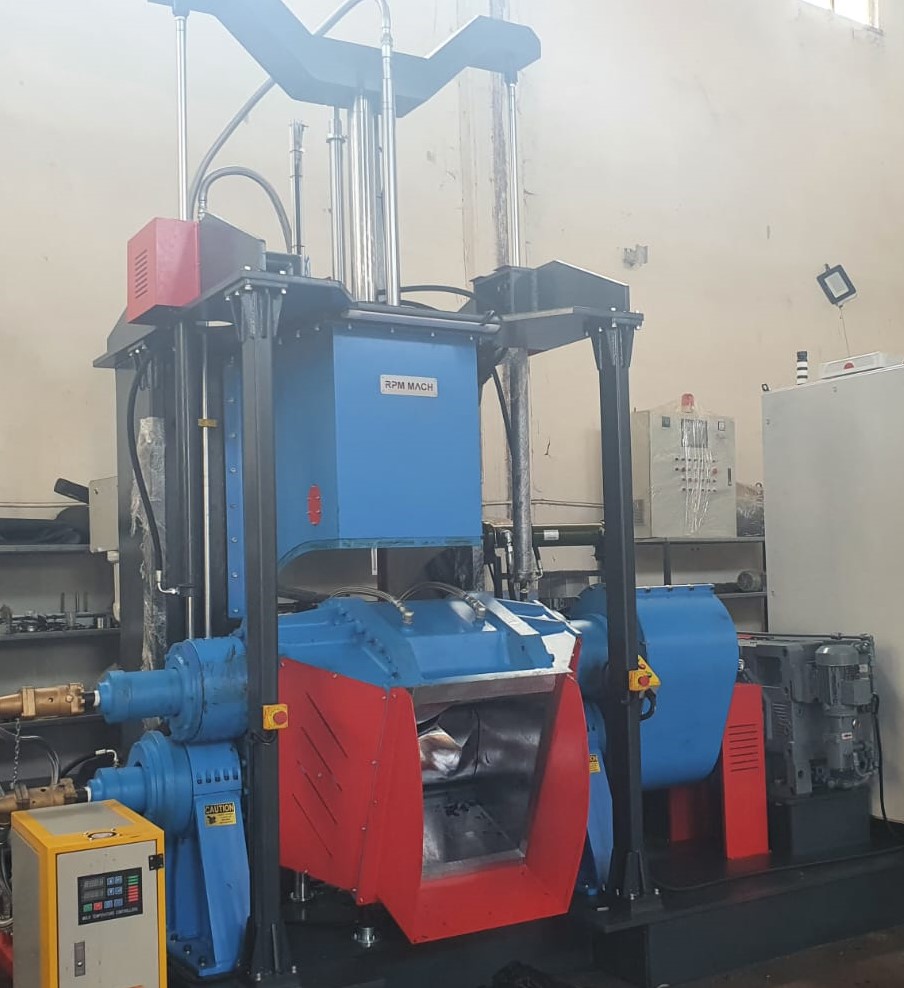
Precision Oil Dosing
An essential feature we highly recommend is our Automatic Oil Dosing system, designed and assembled in-house at RPMMACH. This system ensures precise dosing of oil into the rubber mixer mixing chamber, regardless of the type or quantity required for your formula.
Accurate Dosing; Delivers exact amounts of oil directly into the mixing chamber, enhancing the consistency and quality of your mixtures.
Versatility; Suitable for all types and quantities of oil, making it adaptable to various formulations.
In-House Manufacturing; Designed and assembled by our expert team, ensuring top-notch quality and reliability.
Additionally, we offer production designs suitable for automatic dosing of carbon and other chemicals.
With RPMMACH’s Automatic Oil Dosing system, you can achieve optimal mixing results with unparalleled precision.
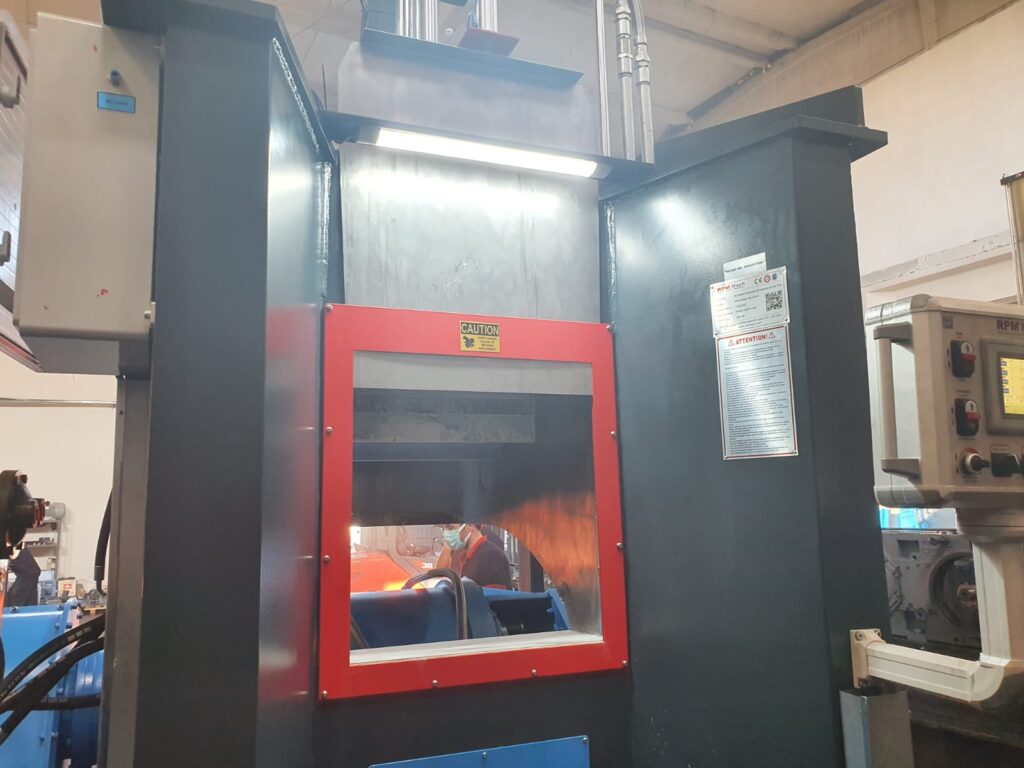
Feeding System
For mixers with capacities ranging from 35 to 350 Liters, the design features front feeding. For mixers with capacities smaller than 35 Liters, the design incorporates rear feeding.
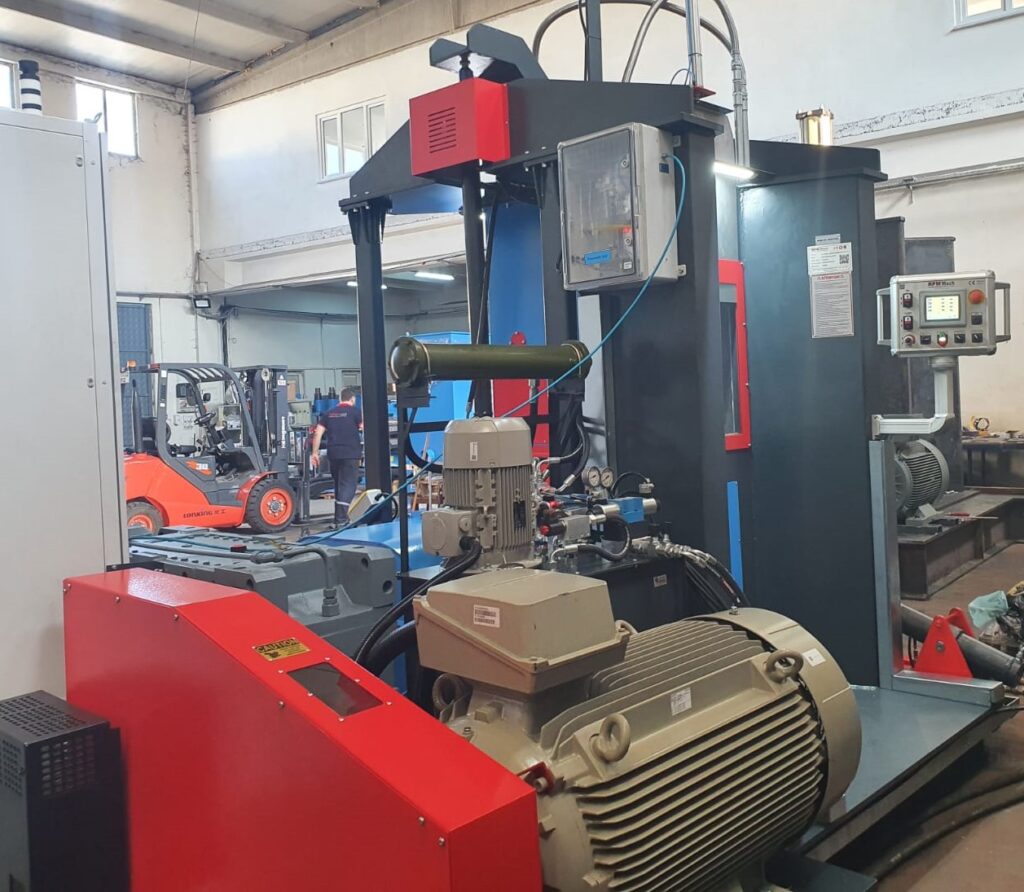
Automatic Ram Pressure Adjustment
RPMMACH’s rubber mixers come standard with an automatic RAM pressure adjustment feature. This innovative system uses the interaction between the power generated during mixing and a special pneumatic valve to press the RAM piston with only the necessary force. This unique feature, exclusive to RPMMACH, acts as a mixing safety measure, ensuring that the rotors, rams, or bearings are never damaged under any strain.
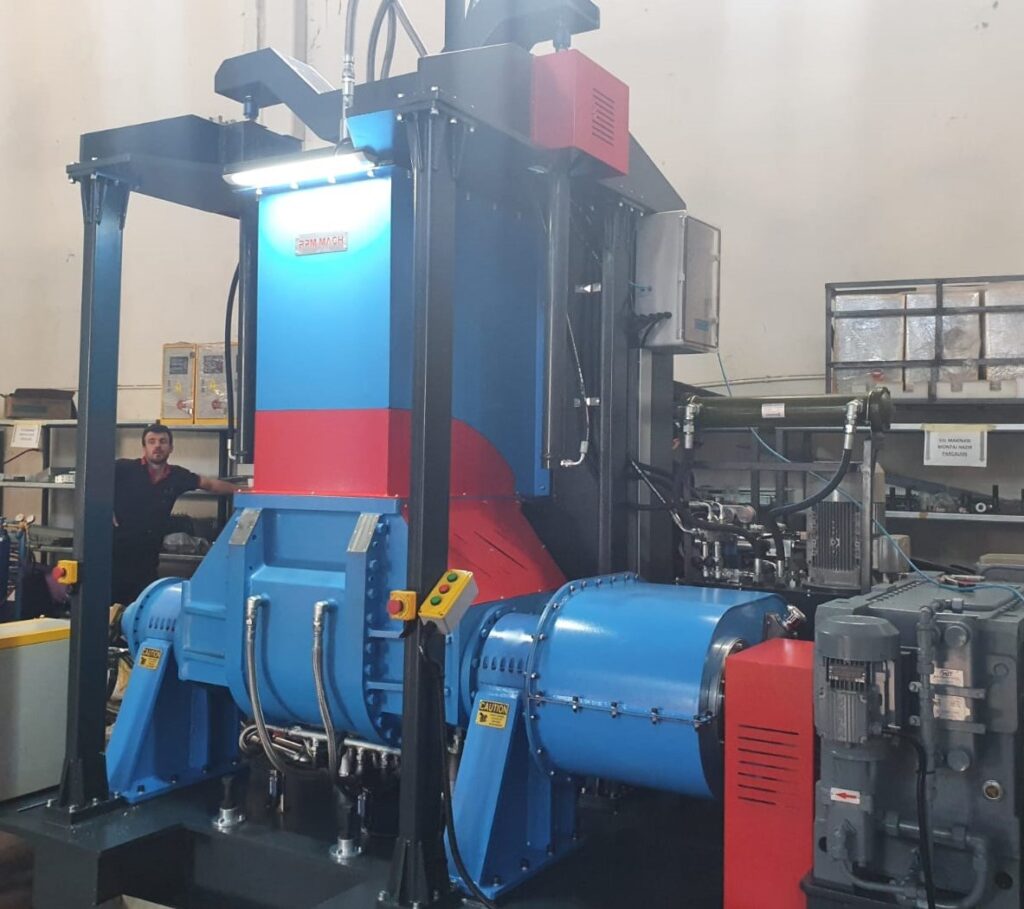
Adjustable Rotor Speeds
Another optional feature is the ability to adjust rotor speeds either automatically or manually with the help of an inverter driver. This capability is particularly useful for sensitive formulas and offers the opportunity to add an accelerator during mixing when needed.
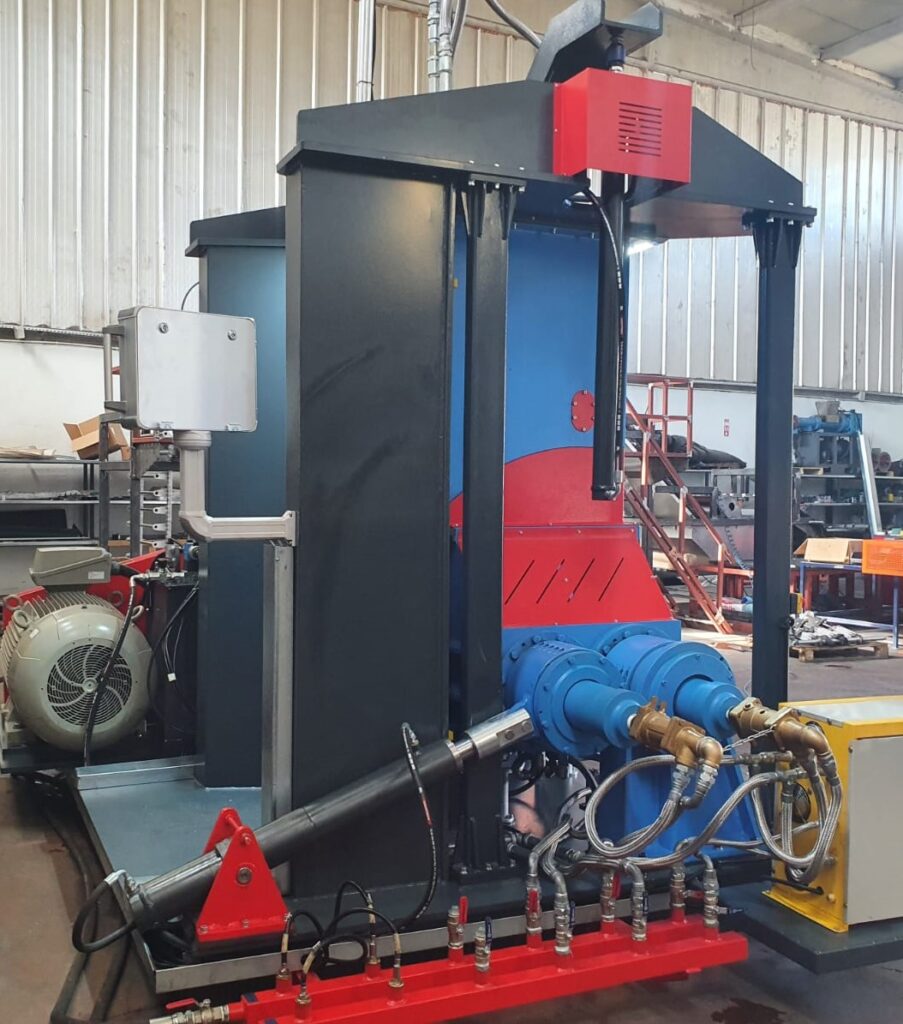
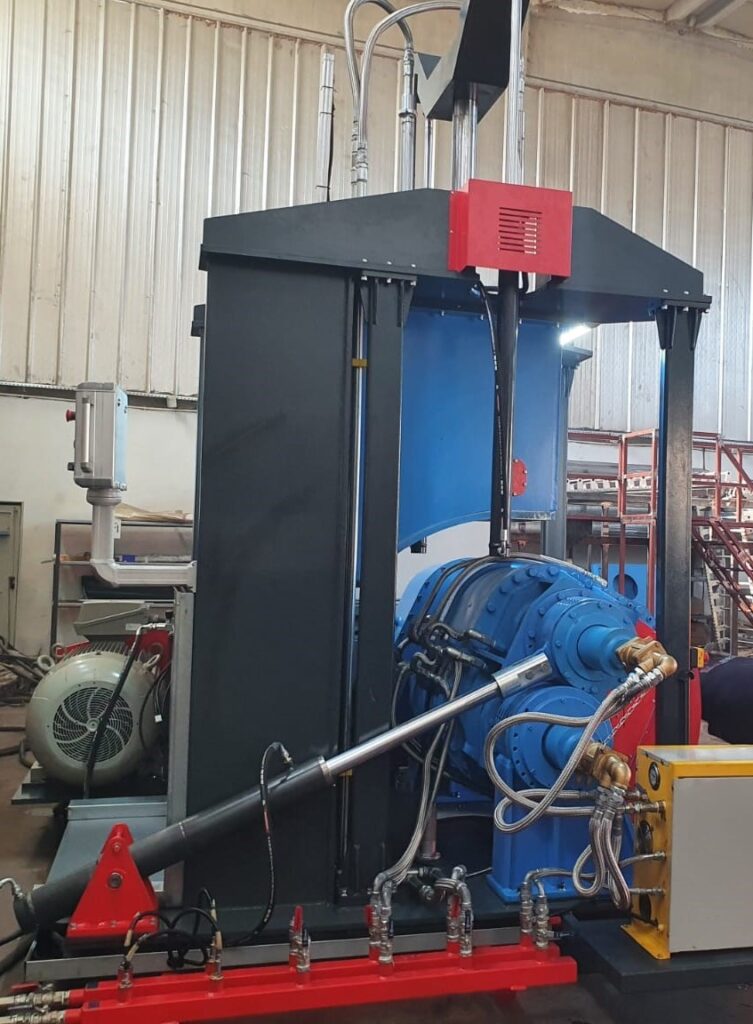
Quiet Operation
RPMMACH’s rubber mixers are equipped with a motor-reducer group that operates very quietly, ensuring a more pleasant working environment.
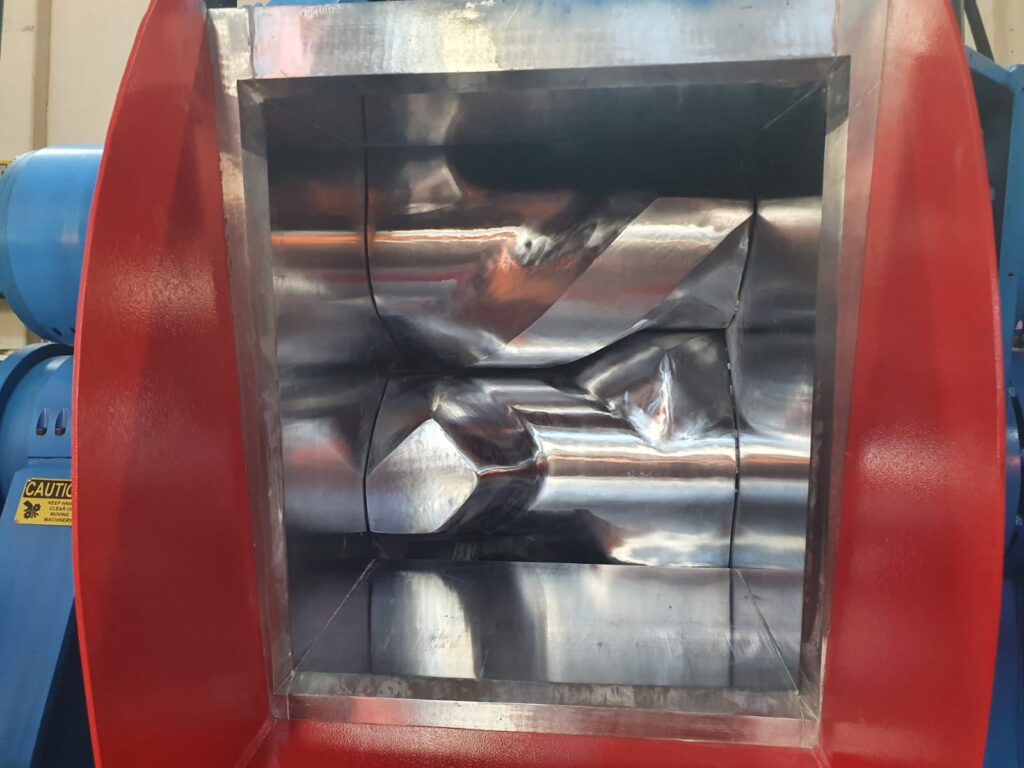
Efficient Machine Cooling System
Our machine cooling system is designed for exceptional efficiency and reliability. It features a pressurized water-cooling system integrated into the RAM, both rotors, and the mixing chamber, ensuring optimal temperature control and performance. Additionally, a standard water-cooling system is utilized in the main reducer to maintain consistent operation and extend the equipment’s lifespan. These advanced cooling solutions help maintain peak performance, reduce downtime, and enhance the overall durability of our machines.
Additionally, the mixing chamber heating system is available as an optional feature, allowing for greater flexibility depending on your specific mixing needs.
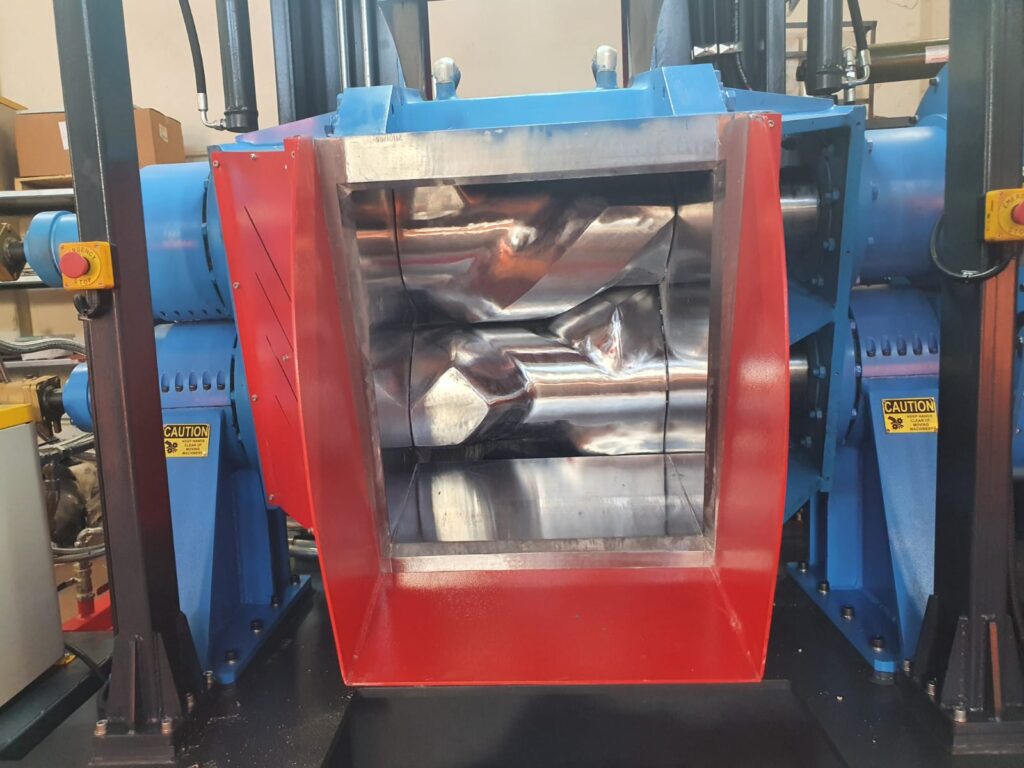
Our machine incorporates high-quality components from renowned manufacturers. All electrical parts are German made, ensuring superior performance and reliability. Additionally, the pneumatic system parts and the specially designed valve for this machine are sourced from Japan, known for their precision and durability.
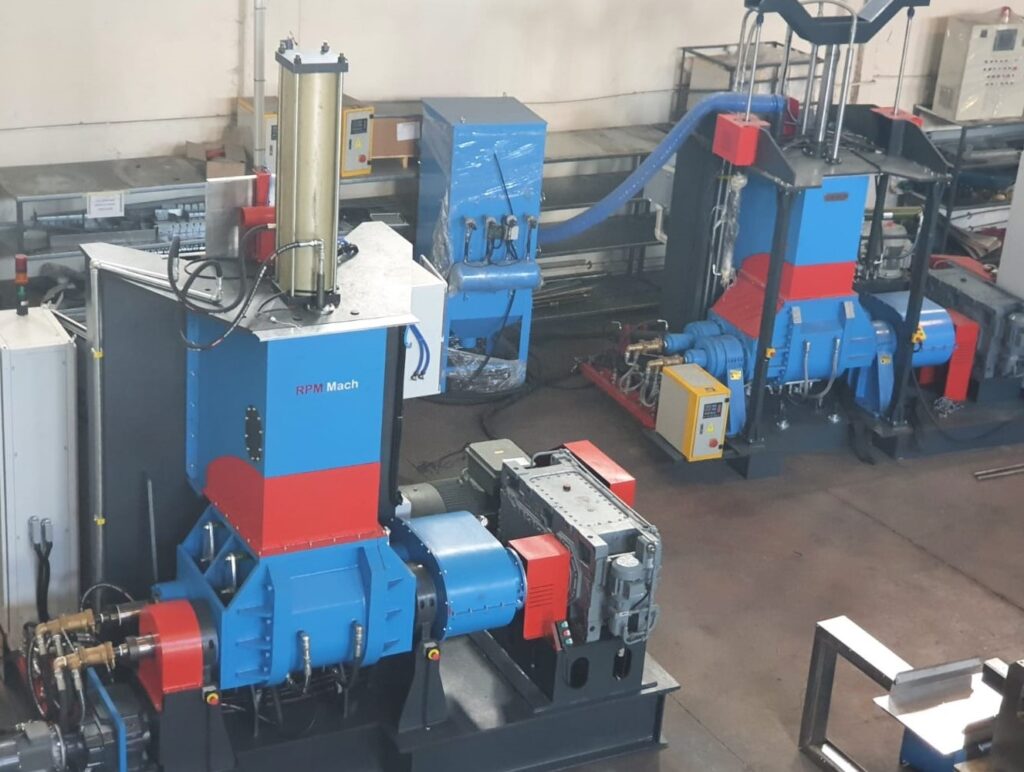
Our machines come in a wide range of standard capacities to suit various needs:
- 1,5 L
- 3 L
- 5 L
- 10L
- 20L
- 35L
- 55L
- 75L
- 110L
- 150L
- 200L
- 250L
- 300L and beyond.
We can also produce machines capable of mixing over 300 L upon request.
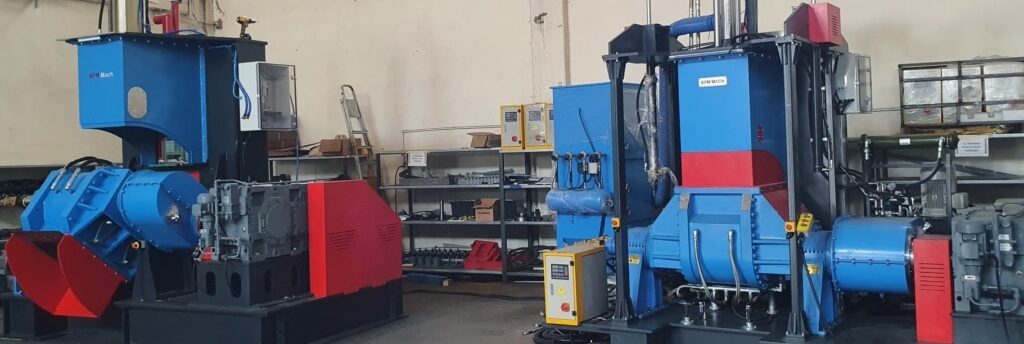
For machines with a capacity of 35 L and above, we recommend using a conveyor for optimal efficiency.