Rubber Extruders and Vulcanızıng Ovens
RPMMACH stands out for its exceptional expertise and success in designing rubber extrusion lines, making us a trusted partner in the rubber processing industry.
The machines used in these production lines vary depending on the specific product being manufactured:
- Rubber Gasket Extrusion and Vulcanization Lines.
- Complete Lines for Rubber Braided Hose (Radiator Hose).
- Rubber Sponge Sheet Extrusion and Vulcanization Lines.
- Butyl Tape Extrusion Lines.
- Silicone Rubber Extrusion and Vulcanization Lines.
- Special Purpose and Custom Design Extrusion Lines.
Rubber Gasket extrusion-vulcanization lines typically include extruders, vulcanization units, pre-shock units, microwave (MW) units, hot air tunnels or salt bath systems, cooling units, silicone application systems, winding units, and other specialized equipment as needed.
The sheet metal door-trunk rubber (Rubber Strip Line) assembly line is a notable success in the automotive industry, widely implemented by many companies in Turkey. This line utilizes the co-extrusion system and can produce multi-component composite head with 2-4 integrated elements. All machinery and equipment for this line are manufactured by RPMMACH. This highly specialized production line features a range of equipment, including extruders, co-extrusion heads, sheet feeders, sheet shapers, tension adjustment systems, shock units, microwave units, automatic hole drilling devices, hot air tunnels, and final shapers, among others.
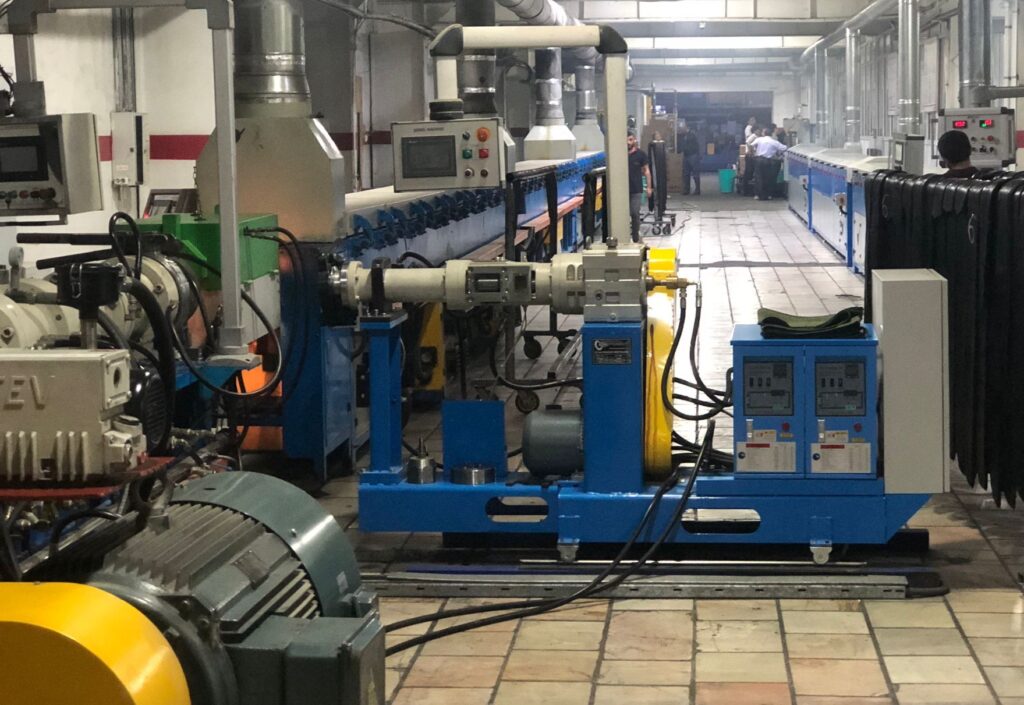
In some instances, a flocking unit can also be integrated into the same line. Recently, a new-generation unit known as the “Plasma-Surface Chrono” has gained popularity for use with these lines. This unit employs a chemical-physical process to provide surface treatment, reducing the friction coefficient between items.
RPMMACH provides machinery for rubber braided radiator hose lines used by numerous companies worldwide These lines typically include the following components: a pin barrel extruder (pin type) tailored for the application, cooling units, a knitting machine, a T-head coating extruder, laser diameter measurement devices, a sprayer unit, a tractor, an automatic length cutting unit, and other specialized equipment as required. RPMMACH’s newly developed FKM-AEM co-extruder and coating system has been introduced as a complete turnkey solution and has garnered significant attention. As is well-known, FKM rubber is one of the most challenging types of rubber to process and extrude in this industry.
The extruders we use for rubber sponge [Foam] sheet extrusion lines are specifically designed for this application. These lines are particularly in demand for NBR-PVC, nitrile, and EPDM rubber types. Following the extruder and the product-specific wide sheet mold, our customized vulcanization ovens can accommodate internal widths of up to 2000 mm. This capability enables the production of rubber sponge sheets with a maximum width of 2000 mm. These products are predominantly used in the insulation and isolation industrys.
Butyl tape extrusion lines typically do not require a vulcanization system. These lines are composed of an extruder specifically designed for butyl rubber, an extrusion mold, a top and bottom tape coating system, and, if necessary, a winding unit. These butyl tapes are commonly utilized in the white goods and automotive industrys.
Silicone extrusion lines are utilized in various industrials, automative products, cable manufacturing, medical products, FDA products, gasket production, and other industrial applications. RPMMACH is a leader in silicone rubber extrusion and vulcanization technology, recently garnering significant attention with its innovative automatic compound feeding system. This advanced system streamlines the process by eliminating the need for manual preparation and continuous feeding of silicone compound. Instead, you can place a predetermined amount of silicone compound (based on extruder size) directly into the feeding hopper, allowing for hands-free operation until the compound is depleted safety.
Silicone extrusion and vulcanization lines generally include components such as horizontal or vertical extruders, T-heads or cable heads, horizontal or vertical high-heat shock units, infrared (IR) ovens, cooling units, length cutting systems, and winding units.
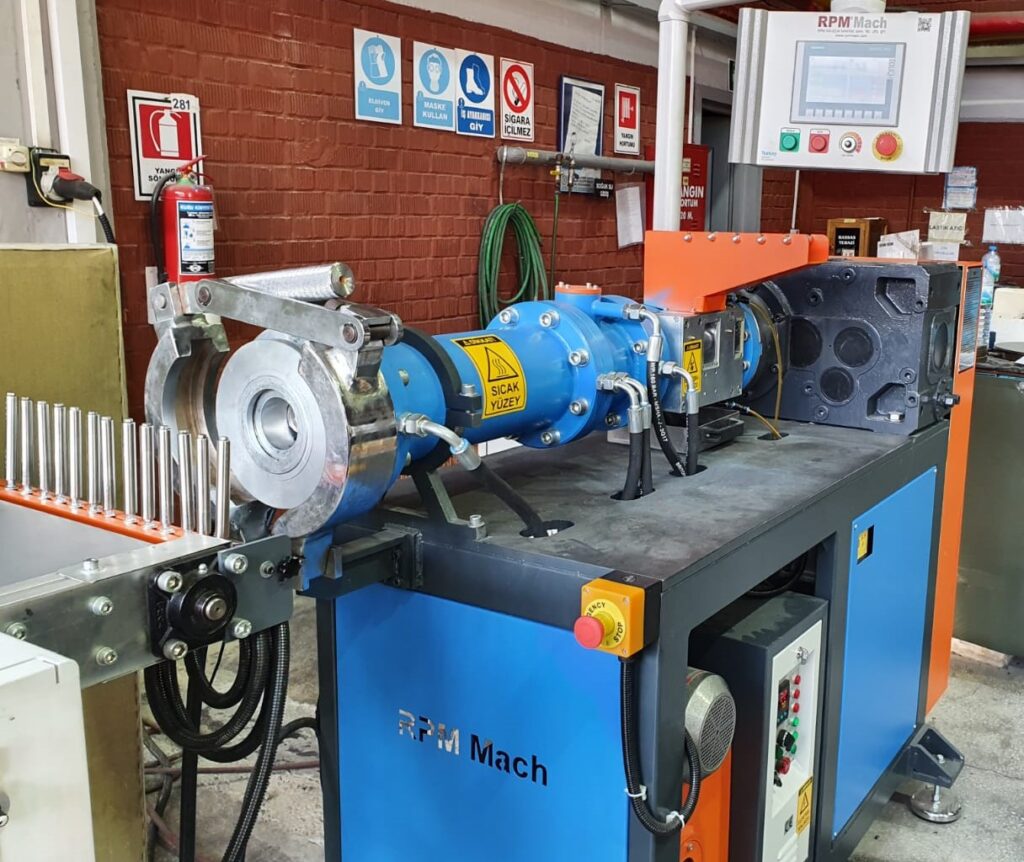
Special-purpose extrusion lines designed by RPMmach are tailored to meet specific customer requirements. These systems can be customized to address various production needs and include options such as:
- Rubber sheet preform production using extruders
- Sheet production with conical extruders and cylinder systems
- Production of rubber sheets with very thin wall thicknesses (as low as 0.5 mm) using extruder and cylinder combinations
- Calender feeding using the extruder method
- Press feeding using the extruder method
RPMmach is equipped to produce specialized extruder systems to suit diverse and unique production applications.
RPMmach offers a wide range of rubber extruders, each tailored for specific purposes and processes. Our extruders are available in various sizes and features, with standard screw-barrel diameters including:
- 70 mm
- 90 mm
- 120 mm
- 150 mm
- 200 mm
- 250 mm
- Customized
We can also produce extruders with standard screw diameters of 250 mm and above, as well as custom intermediate sizes to meet specific requirements.
We typically produce extruders with a screw diameter-to-length (L/D) ratio of 20:1. However, for specific applications—such as radiator hose lines, gear pump systems, CR and FKM rubber processing lines, and other specialized processes—we design and calculate the L/D ratio based on the specific requirements of each process. As a result, we do not provide a standard configuration table for our extruders on our website.
All screws and barrels used in our extruders are manufactured in-house. It is important to note that screws for rubber applications differ significantly from those used for other polymers. These screws, which generally consist of three sections based on the compound transportation requirements, must be meticulously selected for their material composition, surface hardness, and overall quality to ensure durability and performance.
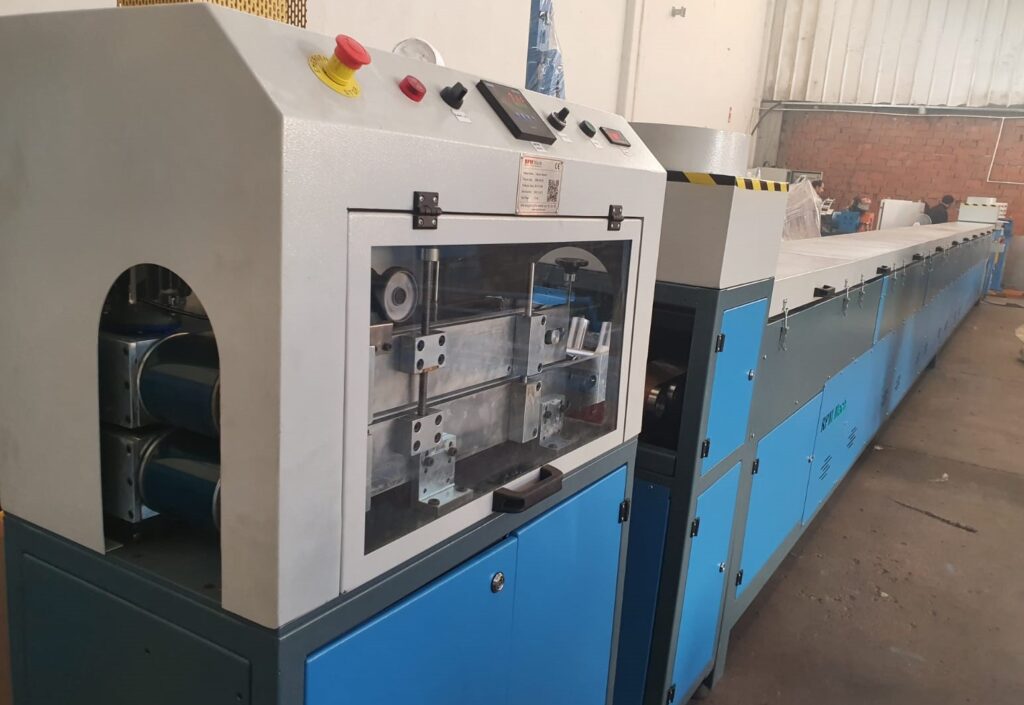
We also manufacture Temperature Control Units (TCUs) in our own facility. These devices precisely regulate the temperature of the extruder screw and barrel to ensure optimal performance.
Additionally, we produce various auxiliary components for extruders, including T-type, Y-type, co-extrusion, hose coating, and rope placement heads. These components are designed for specialized applications, and we have numerous successful references demonstrating their effectiveness.
Our newly developed automatic volumetric feeding system addresses the challenge of preparing and feeding tape-strip paste in silicone extruders. This advanced feeding system has been successfully implemented by many of our customers.
In this new-generation system, silicone paste can be directly added to the chamber in any mass form, depending on the chamber’s capacity. The amount of paste introduced is automatically conveyed to the extruder screw below using two specialized step screws and an adjustable feeding speed. This innovation effectively eliminates the need for manual tape-cutting strip preparation.
In many of our projects for vehicle tire production facilities, we utilize specialized composite-co-extrusion hydraulic head extruders to manufacture tire sidewalls and upper coating components. We produce nearly all components of these high-performance, advanced extruders in-house.
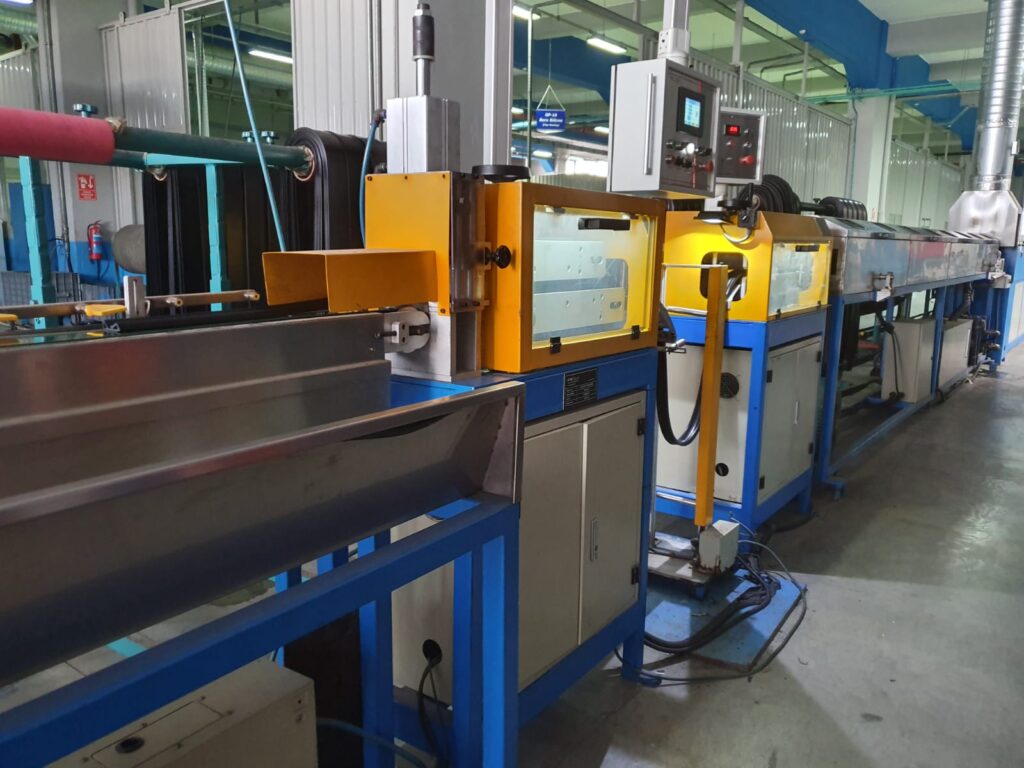
The automatic manufacturing systems we design for rubber radiator hose production lines enhance both product quality and production capacity through a range of advanced options and specialized technologies.
For additional technical details, please contact our company.
For rubber radiator hose production, we typically use pin-barrel extruders, although flat-barrel extruders are also utilized in certain cases. We design these extruders with a minimum L/D ratio of 16:1 to meet specific processing needs.
Hose braiding machines used in these lines are optional and can be selected based on customer preference. The production line can accommodate various brands of hose braiding machines, including those with fixed or variable braiding-head systems.
Our production line includes a sprayer unit that applies a chemical to enhance adhesion properties on the braid. All pulling units feature automatic speed adjustment through potentiometer tension-speed control. Additionally, we design and manufacture the T-head coating system used in the second coating extruder in-house. The cooling and automatic length cutting units are also designed to synchronize seamlessly with the production flow of the entire line.
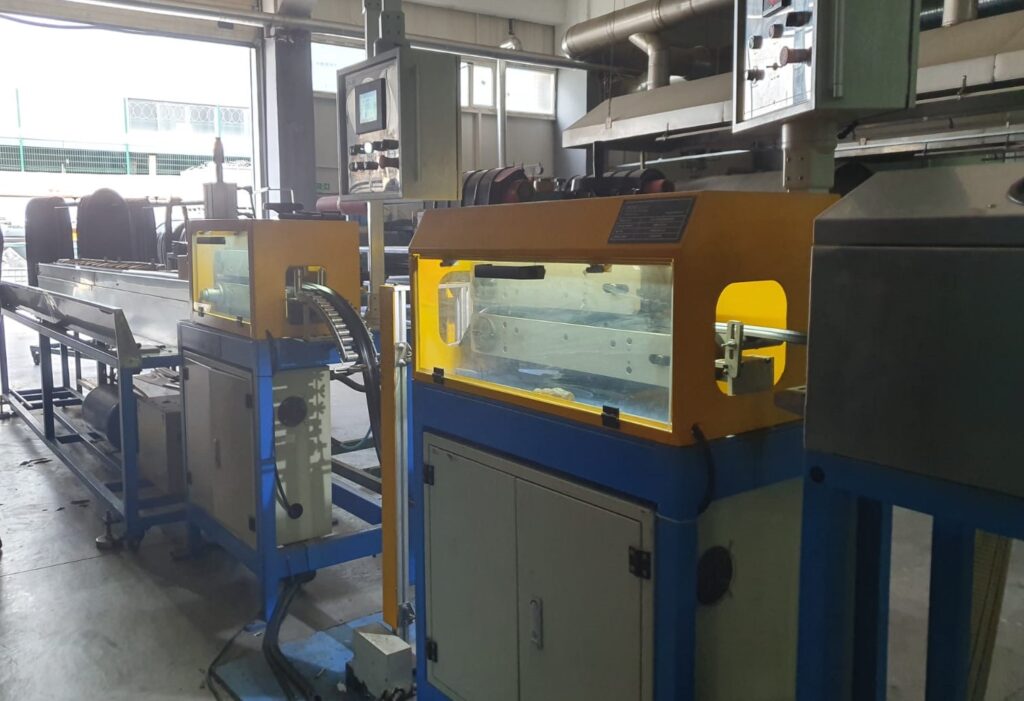
Measurement Precision and Control
For precise measurement control, we offer optional laser diameter measuring devices on the complete production line. These devices enable diameter measurement at both the first extruder exit and after the second coating extruder. All machines and equipment within the line are equipped with individual control panels, and the entire line can also be managed from a single console using a PLC screen.
FKM Rubber Production
Our newly developed extruder screw and barrel, along with advanced gear pump technology, facilitate the efficient processing of FKM rubber in our rubber braided hose lines. Both FKM and AEM rubbers are easily produced using our co-extrusion system, with co-extrusion heads designed and manufactured by RPMmach. Our extruder systems, specifically designed for the challenging processing of FKM rubber, ensure successful and efficient operation.
For more detailed information, please contact our company.
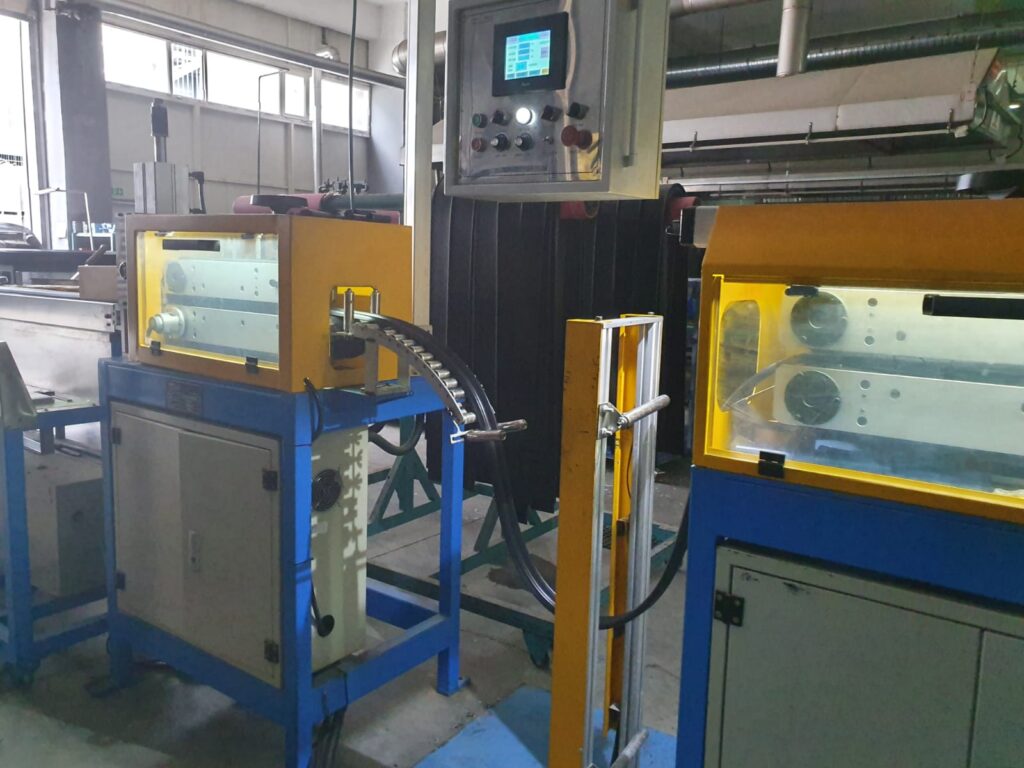
Microwave Curing Rubber Vulcanization Ovens
RPMmach has been designing and manufacturing Microwave Curing Rubber Vulcanization Ovens in Turkey since 2013. These ovens are crucial for the vulcanization of products such as rubber extrusion profiles and gasket wicks. The MW-Frequency system provides uniform heating from the center to the outer edges of the product, preventing deformation and ensuring precise measurement tolerances. MW Curing Units are recommended for applications requiring high precision.
When used in conjunction with standard hot air tunnels, MW curing systems enhance production curing capacity while maintaining precise measurement tolerances. RPMmach prioritizes work and worker safety in the design of MW units, implementing high-security systems and continuously improving safety measures. Our standard MW vulcanization ovens are 9 meters in length, with conveyor belt widths ranging from 100 mm to 300 mm. Custom PTFE conveyor belt widths can be designed upon request, and standard MW frequency power ranges from 8 kW to 18 kW.
For more detailed information, please contact our company.
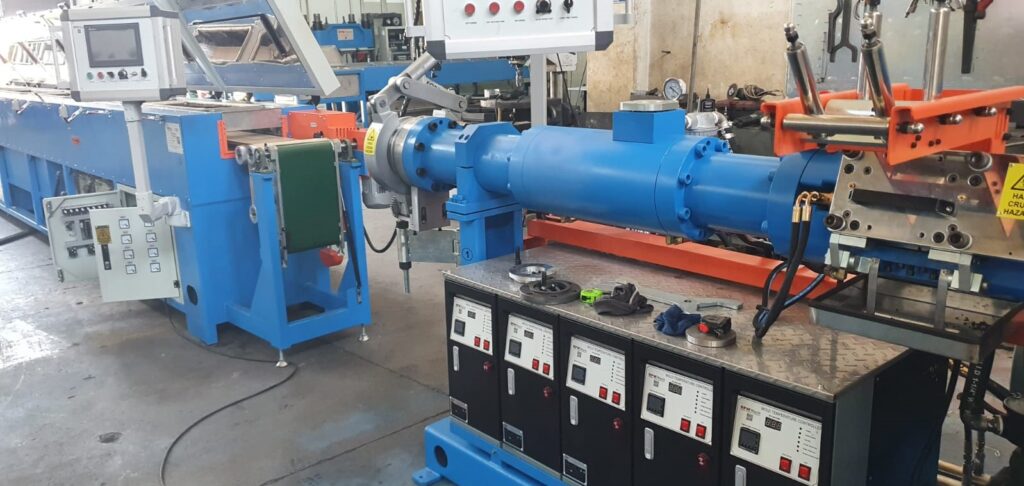
Hot Air Tunnel – Rubber Vulcanization Oven
The Hot Air Tunnel – Rubber Vulcanization Oven is essential for the vulcanization and vulcanization of extrusion profiles. It operates by vulcanizing rubber profiles at specific temperatures for set durations, giving them their final shape. Key features of RPMmach’s Hot Air Tunnels include superior insulation quality and rapid temperature attainment.
Standard units are approximately 9 meters in length, but custom designs are available based on application and project needs. Conveyor belt widths range from 100 mm to 300 mm. Heating systems can be electric or natural gas, with heat distribution optimized by RPMmach’s thermo-dynamic method. Our ovens are designed with the highest standards of work and worker safety and incorporate advanced technologies for ergonomic use and energy efficiency.
For more detailed information, please contact our company.
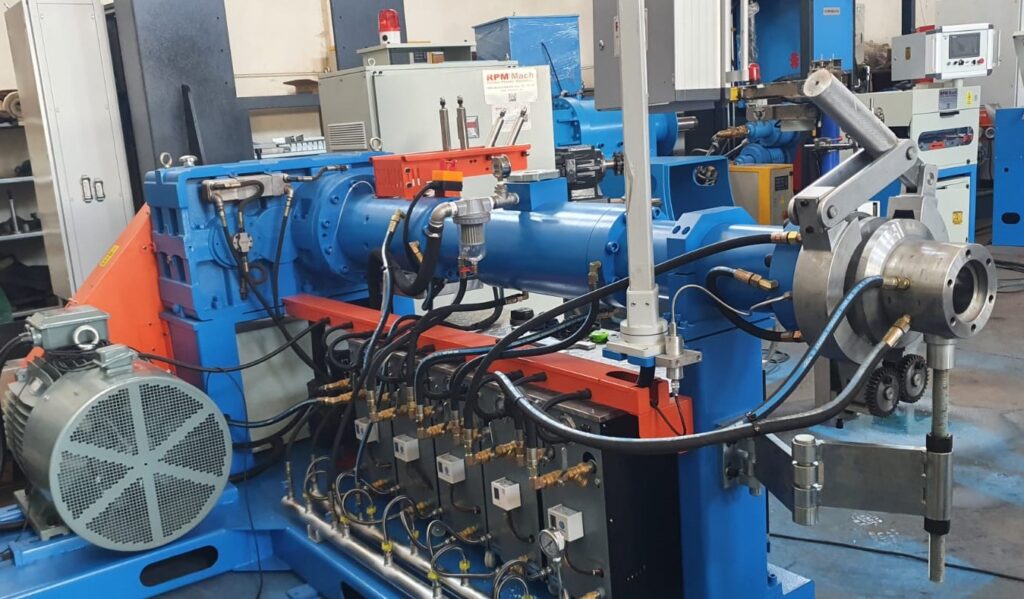
Silicone Extruders and Vulcanization Systems
Silicone extruders and vulcanization systems vary based on application and product type. We offer both horizontal and vertical extrusion systems, with screw-barrel diameters ranging from 30 mm to 150 mm. Special automatic material feeding systems are employed in certain projects.
Effective cooling systems are critical in silicone extruders to manage the temperature of the barrel, screw, extruder head, and feeding system. RPMmach designs these systems to operate with maximum efficiency. High heat-shock units, which can reach temperatures up to approximately 800°C, are used for complete or semi-vulcanization of silicone profiles before they proceed to the IR-Infrared curing ovens.
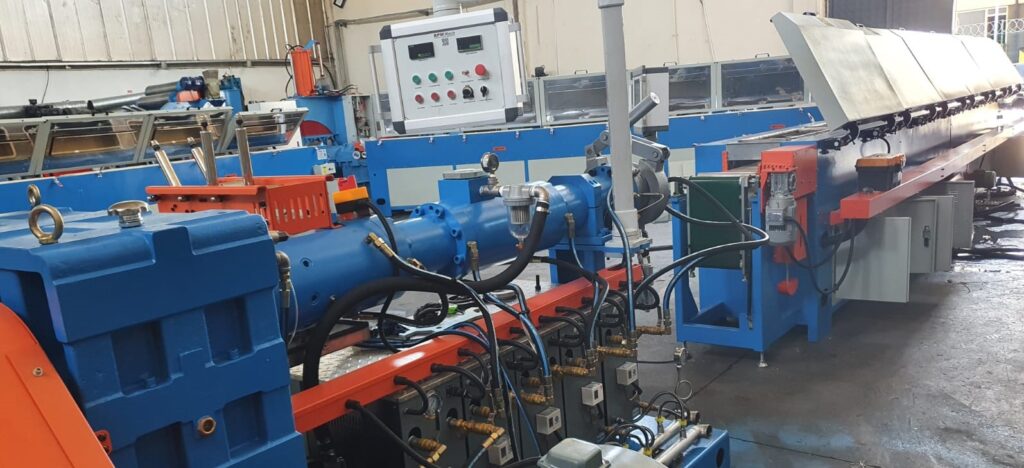
Our IR-Infrared curing ovens, typically manufactured in 6-meter lengths or multiples, feature high insulation quality, rapid temperature attainment, and robust safety options. RPMmach provides comprehensive turnkey solutions, including process technology transfer and training support.
For more detailed information, please contact our company. Sulation quality, fast reaching of the desired temperature, work and worker safety options.
In all machines and complete production projects, RPMmach provides the best service with turnkey assurance, process technology transfer and training support.
For more detailed information, please contact our company.